В последние годы в отношениях Японии и России наметилось существенное сближение. Один из наиболее интересных проектов – аудит российских предприятий специалистами передовых японских компаний. В числе экспертов из Страны восходящего солнца – директор Японской ассоциации по торговле с Россией и новыми независимыми государствами (РОТОБО), генеральный секретарь Японского бизнес-клуба в Москве господин Окада Кунио. Именно к нему мы обратились с вопросом, в чем же особенности российской производственной культуры.


ProКачество: Чем отличается российский подход к освоению философии бережливого производства от классического японского подхода на основе TPS?
О.К.: Принципиальных отличий в подходах нет. Российские специалисты очень тщательно изучают японский опыт и стараются воспроизвести его на производстве. Но структура промышленности в России другая, применяются иные подходы, другой характер отношений между поставщиками и производителем, поэтому скопировать управленческую модель получается не всегда.
ProКачество: Какие проблемы производственных систем типичны для нашей страны?
О.К.:Как я уже говорил, они обусловлены национальными нюансами. Первая проблема – избыточные запасы материалов, сырья и компонентов. Для японцев это выведенные из оборота средства, ненужные расходы на содержание складских площадей. В России же данный подход – необходимость, которая позволяет снизить риск поставки не вовремя. А последнее для вашей страны типично.
В России слишком много лишнего, но русские не готовы от него отказаться
Другая проблема: на российских предприятиях сырье часто хранится не на складе, а, например, на улице. На него воздействуют дождь, снег, перепады температуры. Металлические конструкции подвергаются коррозии, бетон размягчается, пиломатериалы гниют. Но русские не видят в этом серьезной проблемы – они привыкли так работать. В то же время в последние годы на российских предприятиях произошло много положительных изменений, что говорит о внимании производителей к качеству.
Среди сдерживающих развитие российских предприятий факторов также стоит выделить строгое закрепление за каждым сотрудником определенного функционала и зоны ответственности.
Типичный для России пример: водитель везет секретаря, чтобы он передал документы. Почему шофер не может сделать это сам?
Многофункциональных рабочих в России очень мало. Причем офисные работники развивают этот навык в большей степени, нежели производственники. Рабочие же уверены, что не могут выполнить несколько задач разом. Зачастую директор производства и начальник цеха придерживаются того же мнения.
Однако если качественно выстроить систему обучения на производстве, рабочие вполне могут освоить несколько компетенций. Такой подход позволяет повысить эффективность процесса и сэкономить. Если один рабочий выполняет функции десятерых, ему нужно платить вдвое больше. Если же на площадке десять рабочих и каждый четко выполняет одну операцию – это десять окладов. В Японии мы стремимся к многофункциональности, к взаимозаменяемости сотрудников.
На заводе Toyota на каждого сотрудника ведется профайл, в котором фиксируются все обретенные им за время работы компетенции. На основе этого документа руководство может возложить на него дополнительный функционал, которому он уже обучен.
Еще одна даже не проблема, а скорее национальная особенность российских специалистов – нетерпеливость, невнимание к деталям. Японцы другие. Прежде чем начать процесс изменений на производстве, в нашей стране детально проанализируют каждый элемент системы. Приведу пример из японской практики. Производственные линии на заводе Toyota должны быть расположены на определенном расстоянии – допустим, на отдалении девяти шагов. Превышение этого стандарта рассматривается как «потери», или непроизводительные действия. От них нужно избавиться. Русским такой подход кажется избыточным, в вашей стране многие его могут расценить как неэффективную трату времени.
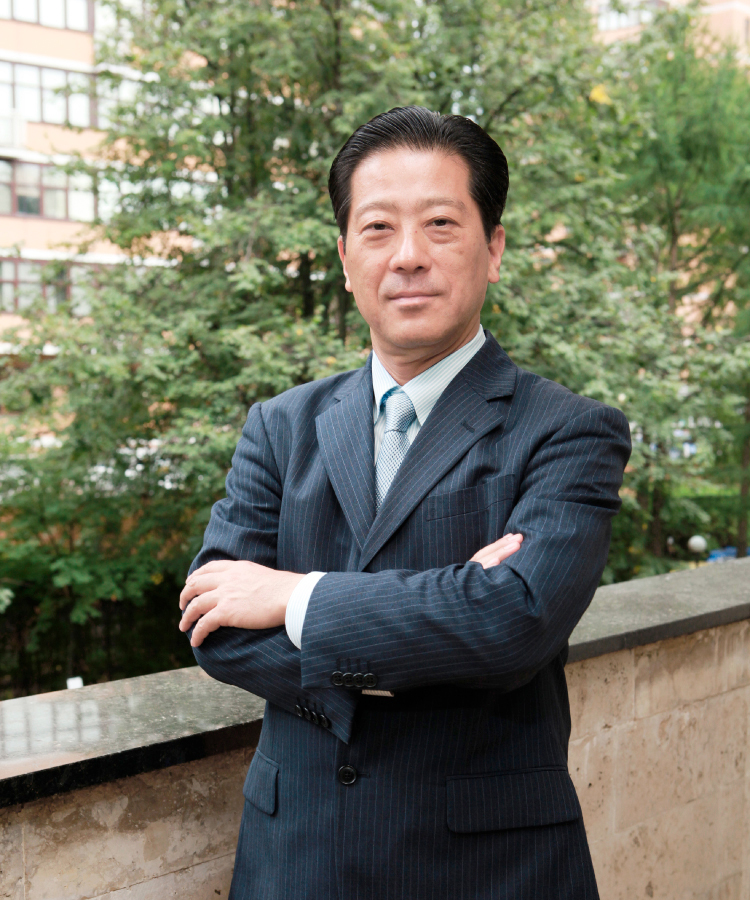
ProКачество: Получается, стремительность и нетерпеливость мешают русским повышать эффективность работы?
О.К.: Русские очень энергичные. При знакомстве с руководителями японских предприятий ваши бизнесмены сразу предлагают создать совместное предприятие и начать общее дело. Это шокирует. Для японцев совместное ведение дел – следствие высочайшего уровня доверия. Сначала нужно познакомиться, обменяться мнениями, оценить потенциал рынка, найти плюсы и минусы организации производства в России, выявить возможные риски. Процесс установления доверительных отношений занимает годы.
Напор российских бизнесменов кажется очень странным, мы не привыкли так работать
С другой стороны, японцы излишне осторожны. Да, мы редко ошибаемся, но, оттягивая момент принятия решения, порой упускаем возможности. В условиях столь стремительно меняющегося мира, что в последние годы проявляется очень ярко, вдумчивость японских бизнесменов превратилась в проблему.
Синергия специалистов из наших стран позволила бы выйти на новый качественный уровень: быстро реагировать на изменение ситуации, принимая взвешенные решения.
ProКачество: Чему еще японские специалисты могут научиться у русских?
О.К.: Широко известным фактом является то, что предприятия черной металлургии по всему миру по сей день используют открытия советских ученых, например непрерывную разливку стали и сухое тушение кокса инертными газами.
Японские технологи, в свою очередь, доработали советскую технологию, в целом усовершенствовали оригинальную разработку. Но при этом я не перестаю рекомендовать японским сталелитейным компаниям активнее сотрудничать с российскими промышленниками, продолжать обмен знаниями и опытом. Японским компаниям не хватает восприятия процессов в целом и общем, а присуща глубокая проработка деталей. Поэтому в этом смысле можно надеяться на взаимное дополнение.
Доведя процесс до совершенства, избавившись от потерь, японцы перестали смотреть вокруг себя. Зациклились на безупречности исполнения существующих процессов.
ProКачество: В России не так давно вышел ряд ГОСТов на бережливое производство. Как вы смотрите на стандартизацию этого подхода?
О.К.: Стандартизация бережливого подхода – мне кажется, это странно. Бережливое производство, кайдзен, предполагает использование очень-очень разных подходов. Унифицировать их нельзя. Вариант организации производства на заводе Honda не подойдет для всех компаний, даже автомобилестроительных. Для каждой отрасли должен быть свой уникальный подход к бережливости. Не стоит ограничивать философию устранения потерь и непрерывного совершенствования рамочными стандартами. Это открытая система. Зарегулированность может навредить.
ProКачество: Какие тренды совершенствования производственной системы Toyota наметились в последние годы?
О.К.: В Японии серьезная проблема – существенное уменьшение численности населения. Нам уже не хватает молодых работников. И проблема будет только усугубляться. Мы вынуждены разрабатывать и внедрять технологии, которые позволят сократить ручной труд. На помощь приходят роботизация, автоматизация, цифровизация.
Если раньше на линии работали десять человек, теперь мы можем рассчитывать только на пять. Нужно либо в два раза повысить производительность оставшихся пяти, либо заменить недостачу роботами.
Японская компания Kawasaki Heavy Industries производит роботов, которые могут выполнять функцию ассистента. Комбинированные участки, на которых роботы работают на одной линии с людьми, уже внедрены на многих производствах. И являются примером успешного взаимодействия машины и человека.
В то же время уже сегодня с помощью роботов можно частично автоматизировать производство автомобилей, что уже сделано на заводах Toyota в Японии, в частности на линиях сварки. Там практически нет людей – лишь наладчики, контролирующие роботизированные системы.
ProКачество: В последнее время очень живо обсуждается тема снижения качества японской продукции. Не так давно прогремел на весь мир
скандал с Kobe Steel. Как вы можете это прокомментировать?
О.К.: Стремление к устранению потерь не всегда способствует повышению качества. Работа выполняется в условиях жесткого плана, процедуры контроля качества столь обширны, что соблюсти их и не нарушить сроки поставки сложно. Пример такой проблемы – ситуация, сложившаяся в Kobe Steel. Я предполагаю, что продукция с некорректными цифровыми данными попала на рынок по причине сокращения циклов проверки качества: допустим, вместо проведения контроля 10 раз по нормативам, по факту проверили только пять.
Мы избавились от всего лишнего. Но иногда это «лишнее» необходимо
Устранение потерь лишило руководство и сотрудников предприятий возможности смотреть по сторонам и адаптировать передовой опыт. Причина проста – нет времени. Это типичный ответ руководителей передовых японских производств.
ProКачество: Российские потребители убеждены, что качество японских автомобилей, произведенных на территории России, значительно ниже, чем тех, что созданы на родине, в Японии. Как вы думаете, обоснованны ли эти предположения?
О.К.: Я, к сожалению, не могу дать ответ на этот вопрос. Однако отмечу, что у Toyota очень много заводов за пределами Японии, и руководство концерна не раз отмечало, что российские работники – одни из самых способных и дисциплинированных из всех, с кем им приходилось работать. Даже японские рабочие иногда пренебрегают правилами, чего нельзя сказать о русских. Они выполняют работу ровно тем способом, которому их научили. Но если не контролировать русских специалистов, качество их работы спустя некоторое время падает. Это в менталитете русских людей. Для решения этой проблемы нужно разрабатывать систему управления и поддержания навыков.
ProКачество: Какие советы вы бы дали российским компаниям?
О.К.: Руководитель организации может сам разработать план повышения производительности, но легче работать с хорошим консультантом или тренером. Пользуйтесь опытом японских специалистов, больше читайте, приглашайте экспертов из тех производственных сфер, которые схожи с вашей. Не надо думать, что консультанты фокусируются только на плохом. Вовсе нет, они находят позитивные моменты, превращая их в точки роста. Причем это не должны быть разовые консультации. Улучшения должны быть поэтапными. При таком подходе производство можно изменить до неузнаваемости. Однако никакой консультант не решит проблемы, если руководители и рядовые сотрудники не понимают целей изменений.
Увеличение производительности – это повышение прибыли компании. Нужно разговаривать с людьми, объяснять, вдохновлять. Если добиться понимания на уровне рядовых сотрудников, улучшения внедряются быстро, легко и эффективно.
Беседовала Ксения Богданова