Бережливое производство, или lean production, уверенно внедряют многие российские предприятия. В 2017 году вышла серия ГОСТов по бережливому производству, но далеко не все специалисты знакомы с этой концепцией. Для молодых профессионалов и компаний, находящихся в поиске оптимального пути повышения эффективности, материал может стать путеводителем в мир lean production.


С чего все началось: от кризиса до концепции
История бережливого производства началась с кризиса в компании Toyota. В 50-х годах XX века в послевоенной Японии бушевал финансовый кризис. Он был связан с истощением финансовых и производственных ресурсов. Единственным способом выживания компаний являлось улучшение качества продукции с одновременным снижением себестоимости.
Именно в этот момент Тайити Оно, прародитель концепции бережливого производства, стал исполнительным директором завода Toyota Motor. Он придумал и внедрил уникальную производственную систему, которая позже стала именоваться Toyota Production System (TPS). Она основывалась на выявлении операций, которые добавляли ценность для потребителя и сокращали непроизводительные затраты. С этого момента начался золотой век компании Toyota, которая успешно вышла на мировой рынок, покорив потребителей соотношением цены и качества своих автомобилей.
В начале 80-х на рынке США появились автомобили Toyota. Они неожиданно быстро стали популярны, перехватив изрядную долю рынка у большой тройки автопроизводителей США. После этого в Японию на завод Toyota отправилась группа американских ученных во главе с Джеймсом П. Вумеком и Даниелем Т.Джонсом. В результате исследований производственной системы «Тойоты» они сформулировали концепцию бережливого производства и изложили ее в своих книгах, которые позже стали бестселлерами.
Хотя концепции lean production и TPS основаны на производственной системе Toyota и их принципы очень похожи, некоторые эксперты различают их следующим образом: TPS – путь конкретной компании, который уникален, а бережливое производство – набор методов, инструментов, механизмов и философия, которые основываются на этом опыте и могут быть реализованы на других производствах
8 видов потерь
Тайити Оно выступал за борьбу с непроизводительными потерями (муда), то есть за уменьшение любой деятельности, которая потребляет ресурсы, но не добавляют ценности для конечного потребителя. Для этого в первую очередь нужно определить операции, повышающие ценность. И это не всегда просто. А затраты на остальные операции надо сделать минимальными.
Рассмотрим пример покраски забора. Рабочий берет со склада краску и кисточку, подходит к забору, окунает кисточку в краску, проводит несколько раз ей по забору, повторяет цикл, регулярно чистит кисточку, в конце рабочей смены он относит оставшиеся материалы на склад, а его начальник проверяет работу. Из всех описанных операций только проведение кисточкой по забору добавляет ценность для потребителей.
Тайити Оно выделил семь основных групп потерь. Восьмую группу сформулировал Джеффри Лайкер. Этот вид потерь также стал каноническим для бережливого производства. Речь идет о следующих видах:
- Перепроизводство. Причины возникновения потерь этой группы – выведенные из оборота средства организации, стоимость аренды складов и зарплата ответственного персонала.
- Ожидание в очередях. Основные источники этого вида потерь связаны с простоем оборудования и персонала, который ожидает поставки необходимых комплектующих.
- Транспортирование. Это потери, связанные со стоимостью излишнего перемещения продукта как на самом производстве, так и от поставщиков/потребителей (износ транспортировочного оборудования, стоимость логистики, появление брака в результате транспортировок).
- Производственные процессы, не создающие добавленной стоимости. Это затраты связанные, например, с добавлением товару функций, не нужных конечному потребителю (холодильник со встроенным экраном), или проведение технических операций, которые не добавляют ценности потребителю.
- Лишние материально-производственные запасы. Данный вид потерь связан с затратами на аренду складов для хранения продукции, на зарплату ответственному персоналу, с рисками превысить срок годности запасов.
- Лишние движения. В данном случае потери возникают из-за того, что сотрудник тратит время на лишние перемещения в рабочем пространстве, поиск необходимых инструментов и т.д. На некоторых участках производства потери времени могут составлять до 20%.
- Потери, связанные с качеством. В этот вид потерь входят потери на исправление брака, утилизацию неисправимого брака и излишние проверки качества изделий.
- Потери от нереализованного творческого потенциала сотрудников. Они связаны с тем, что сотрудник выполняет не свойственные ему виды работ или делает то, к чему у него нет способностей либо интереса. Данные потери чаще всего обусловлены отсутствием инструмента по поиску и поддержке производственных инициатив сотрудников.
Основным способом борьбы с потерями, согласно концепции бережливого производства, служат принципы вытягивания производства и Just in time.
Принцип вытягивания производства подразумевает, что заказ на каждый этап производства приходит от последующего участка производственного процесса (внутреннего потребителя), а начинается все с тщательного изучения потребностей и предпочтений конечного потребителя (внешнего потребителя – клиента). Но в условиях крупного производства этого добиться крайне сложно, поэтому исходящий сигнал подает команда маркетологов, которая оперативно и непрерывно мониторит ситуацию на рынке. Это позволяет избежать потерь от перепроизводства.
Принцип Just in time предполагает, что система планирования и организации работы компании построена так, что все необходимые элементы поступают в производственный процесс в нужный момент и в необходимом количестве. Также этот принцип предполагает бездефектное производство, так как брак может сломать всю четкую систему планирования.
Для реализации концепции бережливого производства применяют широкий спектр методов.
5S
Это, наверное, самый популярный метод бережливого производства. Его суть заключается в рациональной и эффективной организации рабочего пространства. Он нацелен на борьбу с потерями, возникающими в результате поиска нужного инструмента, а также в результате брака из-за неисправного оборудования или неубранного рабочего места сотрудника. В этой системе рабочее пространство рассматривается как индивидуальное рабочее место отдельного сотрудника (от директора до уборщицы), так и производственное помещение в целом.
Метод 5S базируется на соблюдении пяти основных принципов
Seiri – сортировка
Необходимо разделить все предметы в рабочем пространстве на группы:
- всегда нужные: находятся в рабочем пространстве;
- иногда нужны: вынесены из рабочего пространства, но остаются в пределах досягаемости;
- ненужные: должны быть удалены.
Основная идея этого принципа: чем меньше вещей нас окружает, тем легче работать.
Seiton – соблюдение порядка
Для каждой вещи и инструмента должно быть определено свое конкретное место. Этот порядок необходимо поддерживать. Выбор места для инструментов должен проводиться рационально:
- вещь, которой пользуются постоянно, всегда находится под рукой;
- вещи, которые необходимы редко, не должны мешать сотруднику.
Чаще всего при внедрении 5S контуры вещей прорисовываются прямо на рабочем месте, а сотрудники службы качества регулярно проводят аудит рабочего места.
Seiso – содержание в чистоте
Это самый понятный принцип метода 5S. Пыль и грязь провоцируют брак и потери, а следовательно, влияют на эффективность и себестоимость. В большинстве случаев этот принцип трактуют как регулярную уборку не только помещения, но и рабочего места. Однако существуют два нюанса.
- За уборку рабочего места отвечает не только уборщица, но и сам сотрудник.
- Производство нужно устроить так, чтобы мусора и отходов было как можно меньше, и они должны быть локализованы.
Shisuske – стандартизация
У каждого сотрудника должны быть под рукой наглядные инструкции по его деятельности. Они должны быть минимизированы, понятны, визуализированы. Регулярно проводятся стандартизованные проверки технологического оборудования в рабочем пространстве.
Seiketsu – совершенствование
Для существования системы 5S необходимо не только поддерживать уже разработанные механизмы, но и постоянно их совершенствовать. Производственный цикл не стоит на месте, компании меняются, механизмы 5S должны меняться вместе с ними.
В настоящее время появилась система 6S. Она отличается от метода 5S трактовкой последней S. В 5S последний пункт – совершенствование, а в 6S – дисциплина и привычка.
Стандартизация
Этот метод подразумевает создание наглядных инструкций для сотрудников, описывающих основные процессы производства. Инструкции должны регламентировать все операции, которые выполняет сотрудник, максимально коротко, понятно и наглядно.
Максимальный объем инструкций должен составлять 3 страницы, лучше всего – менее одной. Желательно использовать инструкцию с максимальной визуализацией, хорошим примером этого подхода служат, например, инструкции по сборке мебели IKEA, инструкции по охране труда компании «Артис», правила сборки конструкторов LEGO.
Помимо рабочих инструкций, в организации кратко и понятно должны быть описаны все процессы. Для этого, как правило, используются блок-схемы.
Все инструкции должны быть оформлены по единым правилам для всей организации и регулярно обновляться. Руководству следует контролировать выполнение инструкций сотрудниками. В случае выявления отклонений следует провести анализ и определить, почему сотрудник отклонился от инструкций: из-за желания упросить себе жизнь в ущерб производственному процессу или он нашел более оптимальный путь выполнения операций. В последнем случае его опыт следует внедрить в организации, а сотрудника премировать.
Этот метод направлен на уменьшение вариабельности рабочего процесса, снижение количества брака, а также облегчение процесса адаптации новых сотрудников в производственный процесс.
Poka-Yoke
Название этого метода переводится на русский язык как «защита от оплошностей» или «защита от дурака». Он направлен на создание таких условий, при которых сотруднику просто невозможно совершить ошибку, то есть на максимально возможное исключение «человеческого фактора».
Этот метод сугубо практический, поэтому общих принципов для него не существует. Для понимания идеи – несколько примеров:
- Использование конструктивных элементов, которые делают невозможной неправильную сборку всей конструкции. Например, форма SD- или флеш-карт не позволяет вставить их в носитель не той стороной.
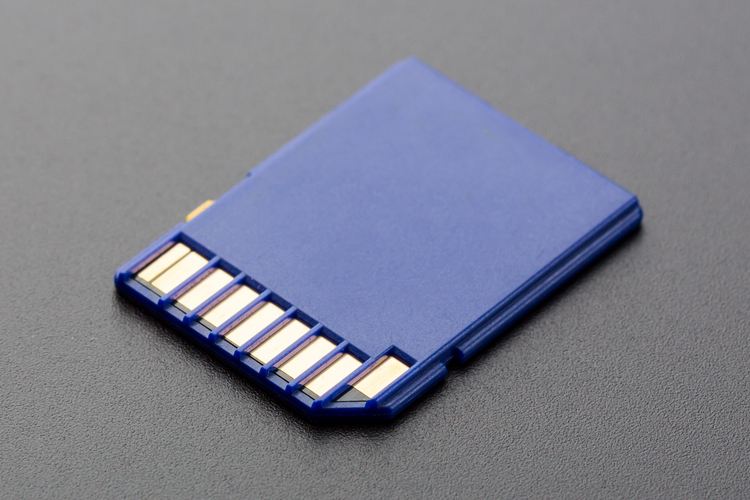
- Цветовая маркировка элементов при производстве. Элементы, которые должны быть соединены между собой, маркируются одним цветом. Например, провод и его разъем маркируются одним цветом: красное к красному, желтое к желтому.
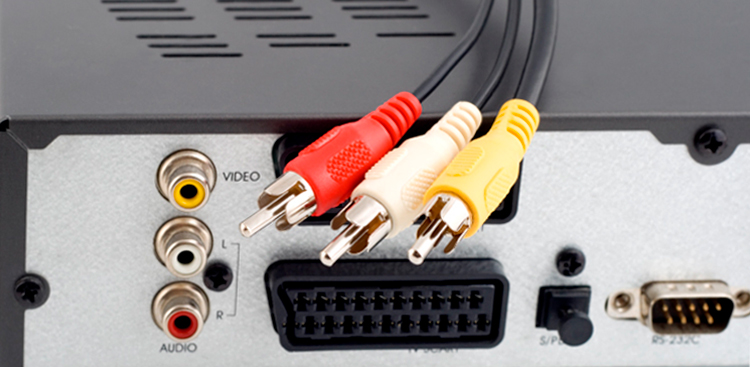
- Автоматизированная система контроля. Создание системы, которая не пропустит элемент на следующий участок производства, если в нем есть брак. Например, на конвейерной линии рабочий должен соединить две детали четырьмя шурупами в сквозные отверстия. После выполнения этой процедуры на ленте установлен фотоэлемент, и, если один из шурупов не закреплен, данный элемент не проходит дальше.
Этот метод также используют для предотвращения производственного травматизма. Например, на конвейерной ленте для распила мебельного щита сотруднику нужно нажать на две кнопки двумя руками. Это сделано для того, чтобы сотрудник не смог при работающей фрезе одной рукой попытаться поправить мебельный щит. Как только он отпускает одну из кнопок, фреза останавливается.
Применение этого метода уникально для каждой отдельной организации, однако игнорировать его нельзя.
Канбан
Это основной метод для реализации JIT и вытягивающего производства. Изначально, это были карточки, которые сотрудник на производственной линии передавал своим внутренним поставщикам, когда у него заканчивались элементы, необходимые для производства. Сейчас исполнителем не требуется передавать карточки, это делает автоматизированная система.
Тайити Оно сформулировал основные правила использования метода канбан:
- Никто не может изготавливать детали без получения заказа на них.
- Карточка канбана должна прикрепляться к любой детали или партии деталей.
Использование метода канбан позволяет:
- добывать информацию о месте и сроках получения и транспортировки продукции;
- предотвращать перепроизводство;
- предотвращать появление дефектной продукции, выявляя, на каком именно этапе происходят дефекты.
Метод быстрой переналадки оборудования (SMED)
Данный метод является сугубо практическим и уникальным для каждой отрасли. Его основная задача – сокращение времени на переналадку оборудования. Это позволит производить детали мелкими партиями, что в свою очередь инициирует применение принципов вытягивания и JIT. Подробно описывать технические решения этого метода нецелесообразно, так как в большинстве случаев они уникальны для каждого предприятия.
Справка
Выше рассмотрены самые популярные, но далеко не все методы и инструменты бережливого производства. Среди не попавших в обзор:
-
6 сигм – методология, направленная на создание бездефектного производства.
-
Кайдзен – система непрерывного совершенствования процессов в организации.
-
Анализ узких мест – методология, направленная на поиск и устранение так называемого бутылочного горлышка в производстве.
-
Пять «почему?» – метод поиска решений возникших проблем.
-
Карта потока создания ценности – инструмент позволяющий выявить операции, добавляющие ценность продукции для конечного потребителя.
-
Всеобщее обслуживание оборудования (TPM) – методология, направленная на увеличение срока службы и эффективности оборудования.
-
Визуализация производства – данный метод нацелен на информирование сотрудников о состоянии производства простыми визуальными средствами, и другие.
Хотя все приведенные методы разрабатывались для производственных компаний, концепция бережливого производства широко используется в сфере услуг, например, в логистике, медицине, ИТ-сфере.
Подробнее о практическом применении бережливого производства читайте в статьях: "От 5S до канбана: методы на все случаи жизни", "Шесть секретов повышения эффективности", "«Технониколь»: мы не внедряем бережливое производство, мы устраняем потери".
